A recent development of the AZTERLAN Metallurgy Research Centre combines real-time monitoring of the manufacturing process and the development of predictive control models to propose the optimal recipe for raw materials based on the available scrap-stock, their cost and their composition.
Melting is a critical stage of the casting process to ensure the manufacture of defect-free parts with assured mechanical properties. The materials and alloying elements that will lead to the target chemical composition are selected in this phase of the process. That is, the “recipe” of the material with which the castings will be manufactured is defined.
The use of recycled steel scrap in the manufacture of cast iron components (such as steel comming from stamping processes) has great economic and environmental benefits. Reusing this material favours the development of a circular economy, making it possible to reduce (and even eliminate) the use of intermediate processed materials, such as iron ingots, with the consequent reduction of environmental impact and economic cost. However, recycled metal scrap has an increasing content of micro-alloying elements that have a great impact on metallurgy and can modify the structure of the castings. In addition, minor elements such as titanium or aluminium, or coatings such as zinc, have a negative impact on the quality of cast components. These elements react with the moulds during pouring and casting process, generating gaseous evolutions that lead to defects on the surface of the iron parts.
In order be able to take action during the melting stage and ensure the quality of the metal at all times, AZTERLAN has developed an intelligent system that allows the optimization of metallic loads based on the availability, the cost and the quality of raw materials, as well as the requirements to be fulfilled by parts. That way, the system automatically proposes a “recipe” that will meet the aimed metallurgical quality.
For this purpose, in real time, this innovative system interconnects information related to the the raw material (recovered of primary metarial) available in the storage silos, the certificates that verify the chemical composition of these materials, their cost and other relevant data comming from the control plan of the plant, such as the characteristics of the metal based on thermal and chemical analyses performed by means of the different techniques available in each foundry. This data are available through a digital twin of the process. On the other hand, and also in real time, an intelligent algorithm monitors both the metallurgical quality and the concentration of unwanted trace elements in the melt, as well as the treatment applied to the liquid metal. With all this information, the optimal mix of raw materials at the lowest cost possible is calculated, by always ensuring that the minimum metallurgical quality to produce each reference is met.
As indicated by AZTERLAN’s head of Intelligent Manufacturing Technologies research line, Dr. Javier Nieves, “in addition to ensuring the reliability and efficiency of the process, the main objective of this development is to reduce as much as possible the cost of the raw material and alloying elements that are necessary to produce the base metal”. That way, “the optimal load to be proposed by the system consists of the one that meets two criteria simultaneously: offering sufficient metallurgical quality to manufacture without defects and doing so at the lowest cost possible”.
This innovative system for the iron foundry offers significant savings in regards with the consumption of raw materials (ingot, scrap, … etc.) and alloying materials, optimizing the overall yield of the process (the ratio between the amount of metal used and parts produced), while having a direct impact in the improvement of rejection rates caused by a low metallurgical quality.
“As a highly complex technology that involves hundreds of interconnected parameters that affect the final quality of components, foundries need to make progress in controlling their manufacturing processes. This is a growing need in the current scenario, in which factors such as energy costs, supply shortage of certain raw materials and the necesity to improve the sustainability of the process require measures aimed at optimizing its efficiency and effectiveness.”
The base-technogy of this application (the Sentinel® Platform developed by AZTERLAN), which must be customized be able to respond to the characteristics and objectives of each organization, is already implemented in several foundry plants, both in the Basque Country and internationally, combining AZTERLAN’s expert knowledge with the specific characteristics and objectives of each foundry plant. Currently, AZTERLAN continues to work on the development of this technology, by incorporating other key concepts and parameters, such as sustainability, when proposing metal “recipes”, as well as defining additions of specific alloying elements.
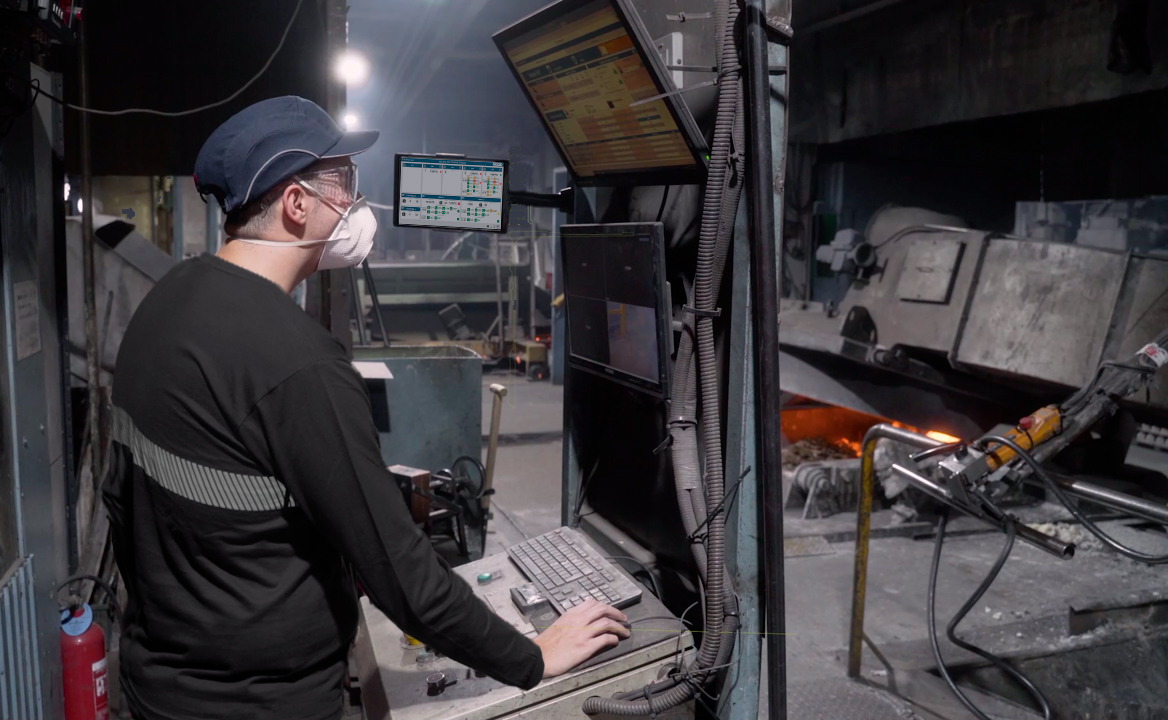
Foundry operator working in a fully monitored melting station