AZTERLAN Metallurgy Research Centre has developed a new patented methodology that allows to produce cast iron components with improved wear and corrosion properties through surface modification technologies. The innovation developed combines the contribution by means of laser cladding of an advanced metallic coating together with a preliminary casting process that conditions the surface of the component, specifically, through an innovative treatment based on metallic powders applied directly in the mould cavity.
The application of surface layers using laser technologies is a widely known technique to improve the characteristics of metallic components manufactured in more conventional materials and manufacturing processes with the main objective of providing improved properties by acting on the characteristics of the surface. In the case of cast iron components, the application of coatings through these technologies is a complex and difficult process that entails some risks that can jeopardize the integrity of the pieces and their ability to work in service: generation of heterogeneous thermal and stress affected areas, porosity or hardened and brittle phases that affect the mechanical properties of the parts, etc.
Although some of these limitations can be overcome by preheating the substrate or multiplying the layers to be applied by laser deposition, these solutions involve a high energy and economic cost and low production efficiency. These difficulties are even increased when dealing with components with complex geometries.
In order to overcome these difficulties, the methodology developed by AZTERLAN alows to prepare the surface of the parts from the casting process for the subsequent direct deposition of coatings using L-DED. For this purpose, a reactive paint has been developed, that applied directly into the mold cavity allows the components to be conditioned from the own casting process.
PhD. Enara Mardaras, responsible for corrosion and materials protection at AZTERLAN, explains that “the reactive paint that we apply in the mold cavity (aplication can be total or in the specific points where we need to generate this reaction in specific areas of the casting), it acts as a ‘primer’ that once the component has solidified, allows us to use laser technologies directly on it. This reactive paint is mainly made up of ad-hoc developed metallic powders made up of different percentages of alloying elements together with a binder element”. In the same way, this methodology considers as well the design of the metallic powders that will be used by L-DED technology and the deposition parameters for the different application scenarios.
The metallic powders used both for the development of the reactive paint and for the application of a coating by means of laser laser technologies have been manufactured at the AZTERLAN Metallic Powder Atomization facilities.
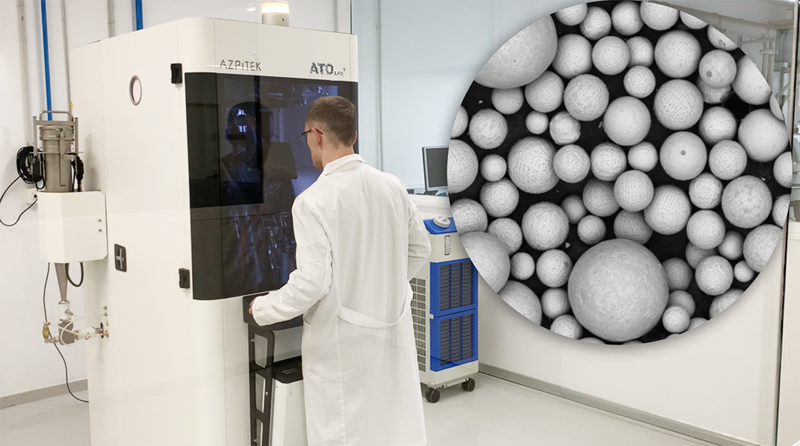
Manufacture of NiTi metallic powders (for the paint applied inside the molds cavity) at the AZTERLAN Metallic Powder Atomization facilities