The VI Heat Treatment Technical Forum, TRATER DAY 2023, that this edition has resumed its face-to-face format, has brought together leading companies in the sector, as well as a significant representation of strategic sectors that apply heat treatments to their products.
In line with the challenges and growing requirements of the industries that manufacture and use metal components, the heat treatment sector faces the challenge of proposing and incorporating innovative and efficient solutions to improve the characteristics and durability of materials and products aimed at highly demanding sectors such as aeronautics, naval or automotive.
With the aim of sharing some of the benchmark innovations for the sector, the TABIRA FOUNDRY INSTITUTE, the AZTERLAN Metallurgy Research Centre and TRATER PRESS held the VI Heat Treatment Technical Forum, also known as TRATER DAY, on October 17th. Around a remarkably technical agenda, the organizers of the event managed to bring together a significant number of companies and industry professionals in a meeting that, after two years, has once again been held in a face-to-face format.
The program was structured around the lectures of top-level technicians and specialists from the companies MONOCROM, ESI GROUP, GH INDUCTION GROUP, NIPPON GASES and OERLIKON BALZERS, as well as the AZTERLAN Technology Centre itself and the WORLD FOUNDRY ORGANIZATION). The meeting, sponsored by ESI GROUP, also had the support of the organizations DEK Durangaldea Empresa Ekimena and EUSKALIT.
After a welcome by the representatives of the TABIRA FOUNDRY INSTITUTE and AZTERLAN, represented consecutively by the Secretary General of I. F. Tabira, José Javier González, and by the General Director of AZTERLAN, Dr. Garikoitz Artola, the session began with a Key Note from the laser manufacturer MONOCROM, by Dr. Igor Alexander, Application Solution Manager of the company based in Barcelona. In his presentation, Alexander addressed the advantages of using diode laser stacks to heat treatment technology, highlighting the “flexibility, modularity and precision that diode lasers in stack format enable for heating applications”.
The general approach was particularized in several case studies applied to a very diverse spectrum of heating sectors and temperatures, which reflected the versatility of laser applications in heat treatments. Among the applications presented, those related to softening processes integrated in sheet metal lines, the generation of plastic ball joint zones in crash components, already assembled in complex chassis assemblies and the surface drying and/or curing processes of paints stood out. Within this casuistry, the MONOCROM expert explained “the enormous advantage of taking advantage of the synergies between conventional heating systems and adaptable laser systems”. He supported this assertion by presenting a use case in which the combination of laser systems with closed-loop control, installed at the outlet of a resistor convective oven, made it possible to adjust piece by piece the end of the curing process by applying thermal power exclusively to the areas that needed it.
The presentation generated the interest of the audience, which was evident in the participatory round of questions in which the application of laser technology for the treatment of thick sections was even discussed.
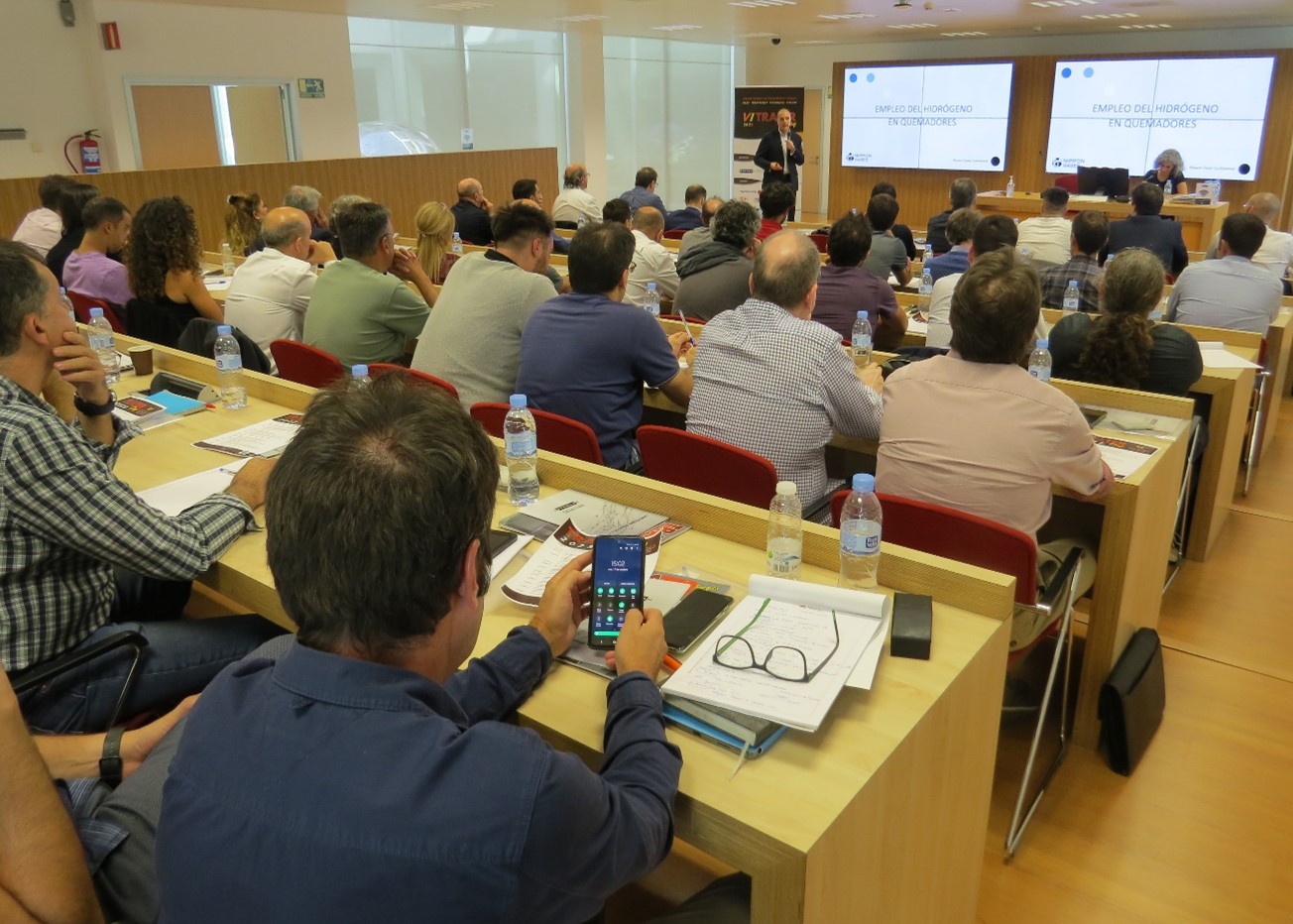
The meeting gathered experts in the field of heat treatments and from companies integrated within the value chain of this industry.
Continuing with another highly topical technology, such as simulation and prediction tools applied to the design and manufacturing process, Igor Pérez Villalobos from the simulation software developer ESI GROUP presented the capabilities and challenges of virtual heat treatment through the use of Sysweld software, developed by the company, highlighting energy efficiency. productivity and increased control over the process.
In the words of the simulation expert, “energy efficiency in order to reduce CO2 emissions”. It is one of the main industrial challenges addressed by simulation to analyse the thermal effects of heat treatment, allowing more efficient and less energy-intensive heat treatment processes to be carried out.
At the same time, with the focus on productivity, the representative of ESI Group explained how simulation “helps reduce cycle times and carry out virtual prototyping, replacing real physical tests with virtual ones and allowing different designs to be carried out in order to minimize thermal cycles that, in addition, help to reduce operational costs”. Along the same lines, and linked to the growing incorporation of automation, digitalization and control technologies for industrial processes, Pérez Villalobos highlighted the opportunities offered by this technology. “Combined with technologies such as digital twins and process control technologies, heat treatment simulation allows for predictive simulation and even real-time simulation aimed at facilitating decision-making.”
The integration of heat treatment simulation with other phases of the manufacturing process was another of the highlights highlighted in ESI Group’s presentation. “We cannot ignore the fact that heat treatments are post-processes that follow other transformation processes, such as forging, stamping or casting. Simulation technologies make it possible to concatenate the analyses of the manufacturing process together with the subsequent heat treatment.”
At the end of his presentation, the ESI Group expert illustrated the different applications of simulation applied to heat treatments through several case studies and stressed the importance of the ecosystem made up of software developers, technology centres and educational centres as fundamental driving and facilitating elements to incorporate heat treatments in the industry.
The next presentation, by Sergio Forner García, Sales Area Manager (Spain and Portugal) of GH INDUCTION GROUP, focused on digitalization and additive manufacturing technologies. In his speech, Forner also highlighted the importance of simulation tools to adapt to new industrial demands and improve the efficiency of processes by promoting “savings in energy costs, working hours and material waste”.
As a technological novelty, the representative of the industrial furnace manufacturing company presented the technology patented by GH to manufacture coils using the EBM (Electron Beam Melting) manufacturing process. In this case, “it is an additive manufacturing process that is carried out in a controlled atmosphere, at a high temperature and is carried out layer by layer”. Forner called this 3D manufacturing technology revolutionary, because of the significant advantages it offers in terms of the ability to develop complex shapes, reduce the weight of coils and save costs. As in the previous presentation, Forner also highlighted the synergies of the concatenation of technologies: “the combined use of simulation of induction processes and EBM printing of the inductors used in the simulated tests has made it possible to reduce the number of iterations of development of induction systems by a factor of three to one”.
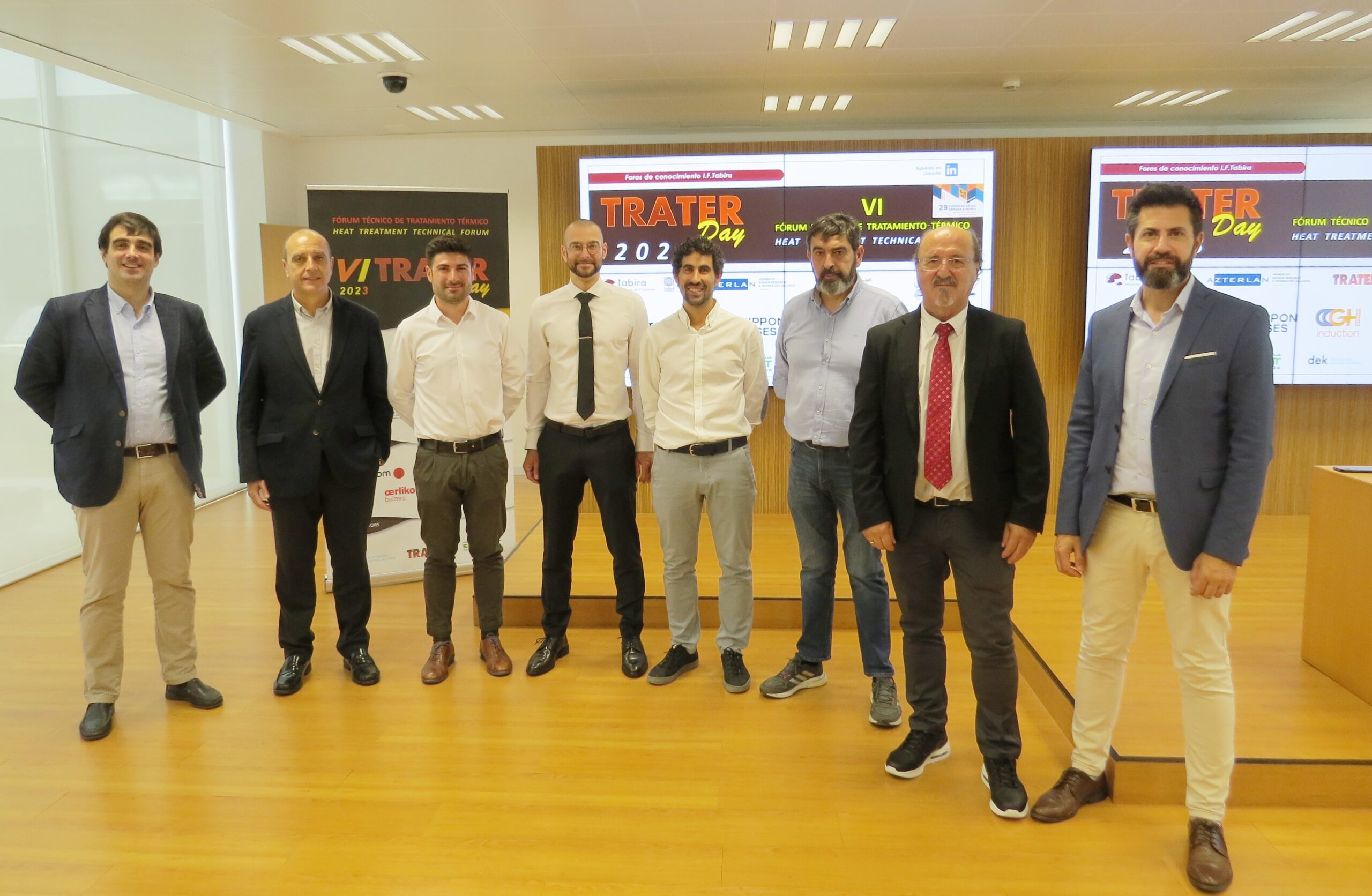
The team of speakers and collaborators of this Heat Treatment Technical Forum.
The last lecture of the morning was given by the AZTERLAN Head of Iron Foundry Technologies, Aitor Loizaga, who shared a presentation on the use of the residual heat accumulated in iron components after casting and using it to carry out a heat treatment of the family of bainitic tempers, without external energy contributions.
As Loizaga explained, “the use of waste heat must be carried out in a very controlled way and requires adapting the chemical composition of the base metal”. Loizaga presented the appropriate cooling profiles to achieve bainitic casting grades, also known as ADI (Austempred Ductile Iron). He explained how, with the appropriate know-how, it is possible to design the chemical composition and the sequence of demoulding and maintenance in an insulating medium that allows homogeneous properties to be achieved, even in components that present significant changes in section.
The foundry expert indicated that AZTERLAN has been developing this type of treatments and high-performance materials for more than ten years, and remarked that, although the concept is simple, its application is not direct, and there are still technical barriers to its use in foundry companies already installed. “Not all molding lines allow access to the molds we want to process at the moment when the component is at the right temperature.” However, Loizaga assured that the benefits offered by online ADI treatment, in terms of costs and delivery times, justify further research and development in this area.
The afternoon session of TRATER DAY 2023 addressed the connection of heat treatment with the reduction of carbon footprint in the industry, a discussion in which the vision of the WFO (World Foundry Organization) through its Secretary General, José Javier González, was presented.
Contextualizing the challenge, González indicated that “the message that greenhouse gas emissions must be reduced is unequivocal. Taken together, the agreements in place have generated increasing pressure for decarbonization across all industrial sectors.” In his words, in order to make progress in this challenge, it seems necessary to systematically study the relationship between the energy structure and CO2 emissions within industry. “The total CO2 reduction depends on the carbon intensity of the electricity supplied. This means that one of the premises for greening the steel industry is the decarbonisation of the electricity sector.”
According to him, between 20% and 50% of industrial energy inputs are lost in the form of waste heat and indicated that factors such as the amount and temperature of heat and the availability of a viable end use are key factors related to the contributions of heat treatment to decarbonization. Thus, the Secretary General of the WFO pointed out that “heat treatment offers great opportunities as a source and as a way to use waste heat. Exhaust gases from the process and heat from the parts themselves can be used as a source. As a use, low-temperature annealing and tempering furnaces can benefit from waste heat flows.”
Within all the possible scenarios in which the adoption of energy efficiency measures overlaps with the recycling of materials and other innovations, he stressed that hydrogen can play an important role in achieving industrial decarbonization goals, although “it is currently an innovation with a high degree of uncertainty and risk due to the challenges it entails, although we are working intensively on it.”
Connecting this global concern to reduce CO2 emissions into the atmosphere, Jorge Visús (Combustion & Heat Treatings Market Manager of NIPPON GASES España, S.L.U.) addressed more specifically the challenges of hydrogen as a fuel.
As Visús reinforced, H2 is established as a possible future source of energy. The European Commission is promoting the use of H2 in industry and, in the short term, the use of natural gas and hydrogen blends as fuel is being considered. Faced with this technological challenge, the gas expert stressed that “it is urgent to develop burners capable of working with mixtures of Natural Gas and Hydrogen, and even with 100% H2”. Energy savings with oxy-combustion burners were also highlighted as an important aspect, where according to the expert “combustion with oxygen saves a large amount of fuel in the heating processes, the higher the outlet temperature of the fumes”.
Regarding the challenges of using hydrogen as a fuel, which in the aforementioned conversation with the head of the WFO was already pointed out as very relevant to meet the challenges of industrial decarbonization in Europe, the head of Nippon Gases identified “the development of burners that allow the use of 100% NG, 100% H2 and any percentage of mixture of both fuels”, as well as the increase in flame temperature, the change in the composition of the fumes, the logistics of hydrogen supply and the cost.
Next, and changing tack in terms of technology, OERLIKON BALZERS COATING SPAIN, represented by its Sales Manager Juan Carlos Cengotitabengoa, shocased the latest innovations in surface solutions developed by the company, PVD (Physical Vapour Deposition) coatings. According to him, these coatings have made great progress in recent years, offering significant characteristics and allowing greater coating thicknesses to be achieved. “PVD stands for physical vapor deposition. To achieve this PVD finish, a process is carried out in a high vacuum and, in most cases, at temperatures between 150 and 500 °C.”
Among the PVD coatings presented by the OERLIKON BALZERS representative are the carbon coatings that provide exceptional hardness 60-70 GPa, high wear resistance and very thin thickness. These coatings are specially designed to meet the demands of aluminium transformation processes, whose growing weight in electric vehicles is serving as an incentive to undertake new developments also in the field of PVD.
The closing of the day came from the hand of Dr. Garikoitz Artola, General Director of the AZTERLAN technology center, who presented a new experimental approach to the study of the impact of heat treatment variables on the properties of alloys through a practical case. More specifically, this second AZTERLAN presentation focused on high-performance test batteries, which allow a large number of process conditions to be tested, minimizing the investment of resources necessary for this purpose.
In Artola’s words, “we consider this new method to be so promising that we are in the process of publishing it in detail in a high-impact scientific journal for the benefit of the research community.” Thus, the presentation allowed the public present at the conference to advance these innovative laboratory practices that have not yet been published in open access.
The proposal presented by the AZTERLAN expert consists of a combination of Jominy tests with the Small Punch Testing technique, which in the case that served as the guiding thread for the presentation, proved to reduce by up to an order of magnitude the resources used to study the impact of quenching and tempering treatment conditions on the mechanical properties of steels. However, he also pointed out that “there are improvements in testing capabilities, since one of the great benefits, beyond the productivity achieved, is the resolution obtained in the hardening speeds. We are able to discriminate very small variations in the cooling rate.”
The results presented at the meeting have already begun to be used in industrial cases, despite the fact that they are part of a doctoral thesis still in progress, developed by Ibon Miguel, a researcher at AZTERLAN, under the co-supervision of Artola himself.
By way of conclusions, the organizers of the event highlight that this latest edition of the Heat Treatment Technical Forum reinforces the need and interest of the sector to continue betting on innovation, being aware of the critical role it plays in the production of highly demanding metal components. Having face-to-face meeting points that allow them to share and discuss concerns, trends and technological challenges to continue improving their competitiveness and their contribution of added value to their value chain is a key aspect. “After a period strongly marked by the pandemic, in which we had only been able to hold this meeting online, we have been able to see that, in addition to the technical content, the sector has responded positively to the idea of meeting again and sharing and discussing in person.”