El Centro de Investigación Metalúrgica AZTERLAN ha desarrollado una metodología bajo patente que permite aportar a los componentes de hierro fundido propiedades mejoradas al desgaste y a la corrosión, a través de tecnologías de modificación superficial. La innovación desarrollada combina la aportación mediante laser cladding de un recubrimiento metálico junto al proceso de preparación previa de la superficie del componente actuando sobre las características del proceso de fundición, concretamente, mediante un tratamiento innovador basado en la aplicación de polvos metálicos sobre la cavidad del molde.
La aplicación de recubrimientos mediante tecnologías laser es una técnica ampliamente utilizada para mejorar las características de los componentes metálicos fabricados en materiales y procesos de fabricación más convencionales, en los que se busca aportar un beneficio actuando sobre las características de la superficie. En el caso de los componentes de hierro fundido, la aplicación de recubrimientos mediante estas tecnologías es un proceso complejo y difícil, que conlleva algunos riesgos que pueden poner en jaque la integridad de las piezas y su capacidad de trabajo en servicio: generación de zonas de afección térmica y de estrés heterogéneas, porosidad o fases endurecidas y frágiles que afectan directamente a las propiedades mecánicas de las piezas, etc.
Aunque algunas de estas limitaciones pueden ser superadas mediante un precalentamiento del sustrato o multiplicando las capas de aportación por deposición laser, se trata de procesos con un alto coste energético y económico, con una baja eficiencia productiva. Estas dificultades se ven incrementadas cuando se trata de componentes con geometrías complejas.
Con el fin de superar estos problemas, la metodología desarrollada por AZTERLAN consigue preparar la superficie de las piezas moldeadas desde el propio proceso de fundición, para la posterior deposición directa de recubrimientos mediante L-DED con todas las garantías. Para ello, se ha desarrollado una pintura reactiva que, aplicada directamente en la cavidad del molde de arena en el que se colarán las piezas, permite acondicionar las propiedades de los componentes desde la colada.
Como explica la Dra. Enara Mardaras, responsable de corrosión y protección de materiales de AZTERLAN, “la pintura reactiva que aplicamos en la cavidad del molde, bien sea en toda la oquedad o en puntos específicos de la misma si solo necesitamos generar esta reacción en zonas específicas de la pieza, actúa como un ‘primer’ que, una vez solidificada la pieza, nos permite el uso de tecnologías láser sobre la misma de forma directa. Esta pintura reactiva se compone, principalmente, de polvos metálicos desarrollados ad-hoc compuestos por distintos porcentajes de elementos de aleación, junto con un elemento aglomerante”. Del mismo modo, esta metodología contempla también el diseño de los polvos metálicos ad-hoc que serán aportados mediante tecnología L-DED y los parámetros de deposición para los diferentes escenarios de aplicación.
Los polvos metálicos utilizados tanto para el desarrollo de la pintura reactiva como para su posterior aplicación mediante tecnologías laser han sido fabricados en las instalaciones de Atomizado de Polvos Metálicos de AZTERLAN.
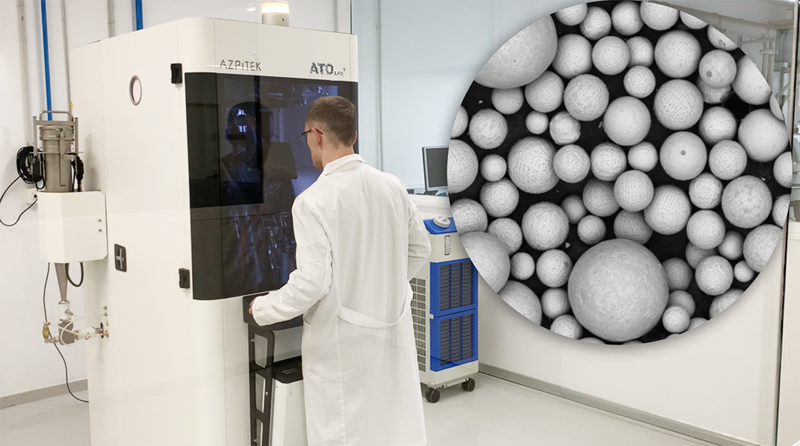
Proceso de atomizado de los polvos metálicos NiTi, utilizados para el desarrollo de la pintura aplicada en la cavidad de los moldes, en las instalaciones de AZTERLAN.